Aluminium is a metal that can be shaped into a wide range of products. It is ly versatile, lightweight, and resistant to corrosion. These characteristics make it a popular choice for use in a wide range of applications. One of the common processes for forming long pieces of aluminum into the shapes that they need to be is extrusion. This process can be done using either hot or cold methods.
In the case of
aluminium cold extrusions, the process is conducted at room temperature or a slightly warm temperature. The resulting product is stronger and more durable than that produced through hot extrusion. It also requires less energy to produce and results in a much more environmentally friendly production environment. This type of aluminium extrusion also has the advantage of producing a finished product with very little oxidation, which is not possible in the hot extrusion process.
The basic process of extruding aluminium is to form a solid piece of the metal into a long, durable shape by applying pressure. The common type of extruded aluminium is tubing, which is created in a number of different ways. The method involves forming the tubing by welding together several sections of the aluminium. This is often used to create large tubes that can hold pressured gases or liquids.
Another way to produce tubing is to draw the aluminium through a die using its own tensile strength. This method is often used to produce wire and bars of aluminium. This is a quicker and cheaper option than the extrusion process.
Both types of extrusions can be formed into a wide variety of shapes, and are then subjected to additional processing. This can include cutting the profiles to their final lengths, heat treating them to improve their tensile strength, and coating them with various finishes to enhance their appearance or resistance to corrosion.
The common uses for extruded aluminium are found in the aerospace, automotive, building, and transportation industries. They are also used in electrical and electronic equipment, where their ability to conduct heat is important. Other industries that commonly use aluminium extrusions include furniture and sporting goods. These materials are also ideal for protecting objects from infrared radiation, visible light, and radio waves. In addition, they are non-sparking and non-magnetic, making them useful in environments where explosive or flammable material is present. The versatility of aluminium also makes it an choice for use in a wide range of consumer products. These benefits make aluminium extrusions a popular choice for designers and manufacturers of all kinds. To learn more about how to work with these components, contact an expert at an extrusion manufacturing company. They can provide valuable insights into the extrusion process and help you select the right profile for your application. You can even request a sample of an extrusion to see how the finish and color will look before you place your order. This will help you avoid any surprises once your order is placed.
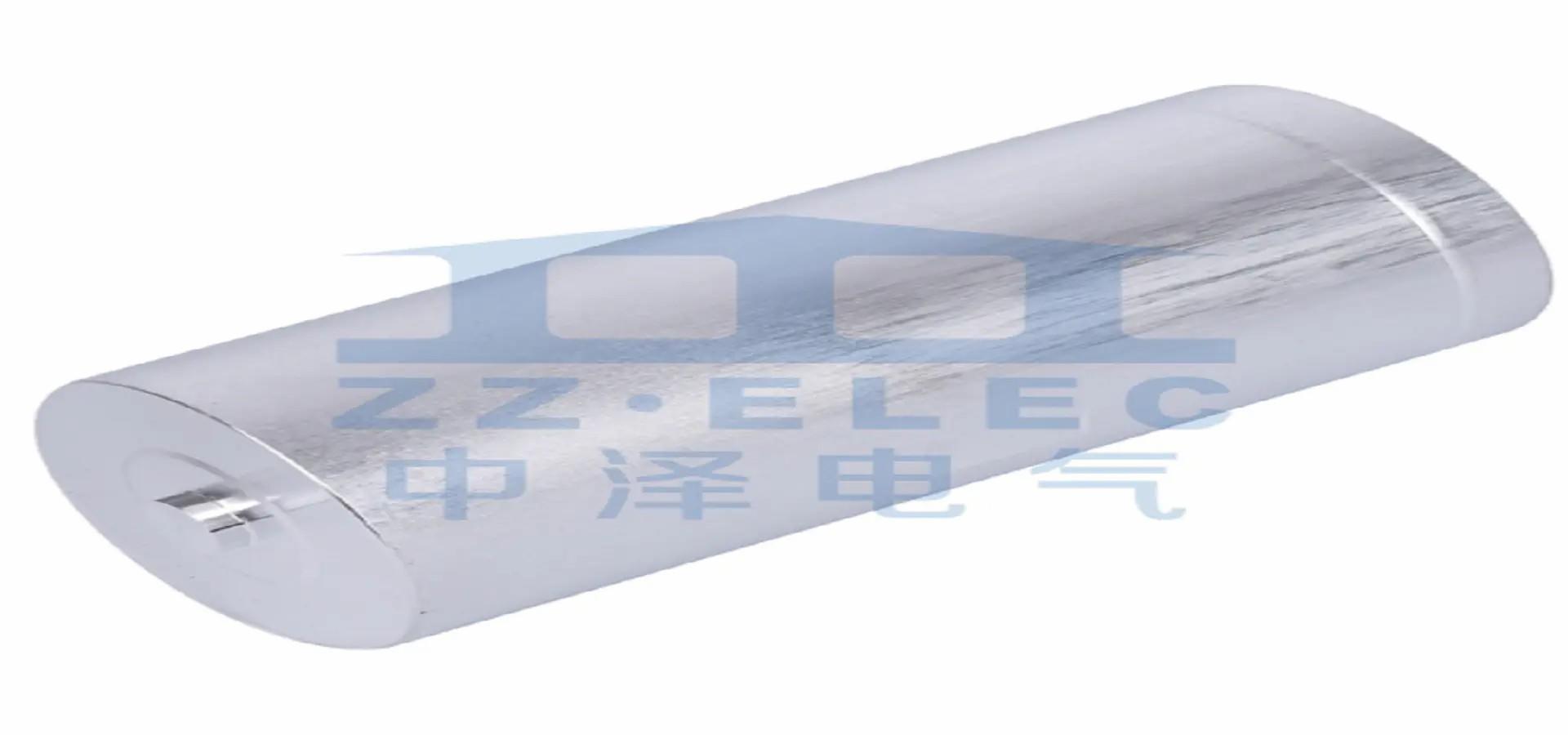